2.1 Sludge Thickening
Sludge thickening is a process that involves separating and removing some of the liquid from sludge to increase its solids content and reduce the overall volume. Thickening is generally accomplished by physical means.
The following thickening methods will be discussed in further detail:
- Gravity Thickening
- Flotation Thickening
- Centrifugation
- Gravity Belt Thickening
- Rotary Drum Thickening
However, some of the technologies mentioned may not be very suitable for emergency settings because of the high CapEx, OpEx, or complexity.
A detailed overview of thickeners and experiences with faecal sludge can be found in the following publication:
Gravity Thickening
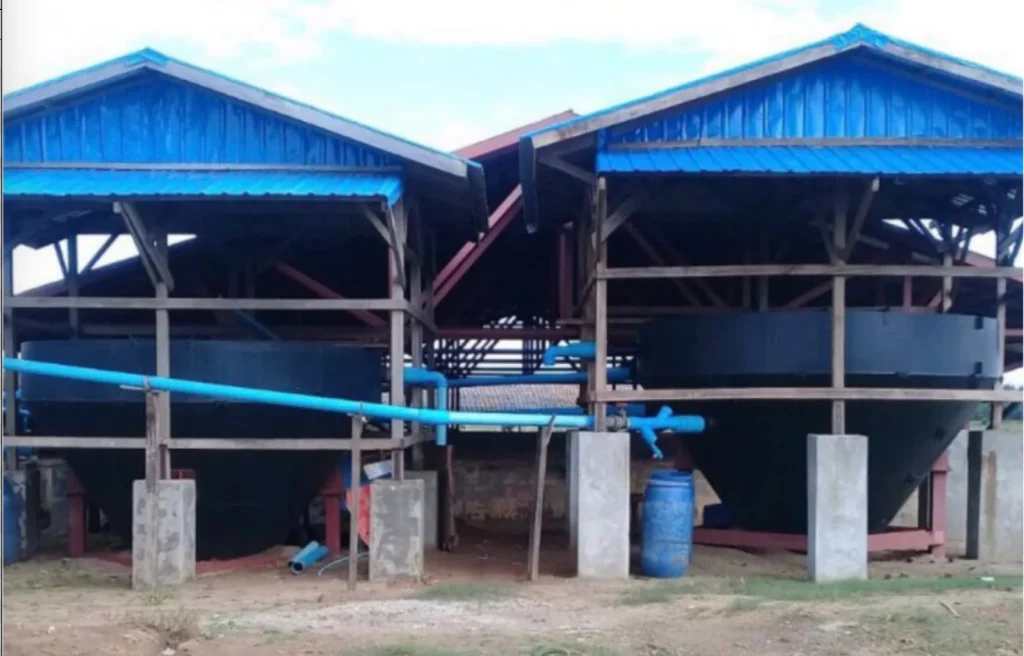
Gravity thickening is a widely used technique for dewatering and concentrating sludge before digestion. It is a simple and cost-effective method compared to other thickening methods. There are two types of gravity thickening: plain settling and mechanical thickening.
In plain settling, scum, composed of floating materials such as grease, oils and other low-density particles, forms on the surface and sludge, consisting of heavier particles and high-density solids, settles at the bottom. Subsequently, the scum layer is skimmed off, and the settled sludge layer can be scrapped towards a collection point and removed by pumping or suction.
A typical mechanical thickening setup consists of a slow-rotating circular tank with a sludge collection system. Mechanical thickening is achieved by gently agitating the sludge, while open channels allow the effluent to escape. Sludge conditioning with organic polyelectrolytes such as anionic, non-ionic, and cationic can increase sludge settling rates.
The sludge’s expected total solids (TS) concentration after thickening is 2 – 15%, depending on residence time. The process does not require any conditioning of sludge with polymers or flocculants. However, especially regarding plain settling, the efficiency can be improved, and residence time can be reduced.
Flotation Thickening
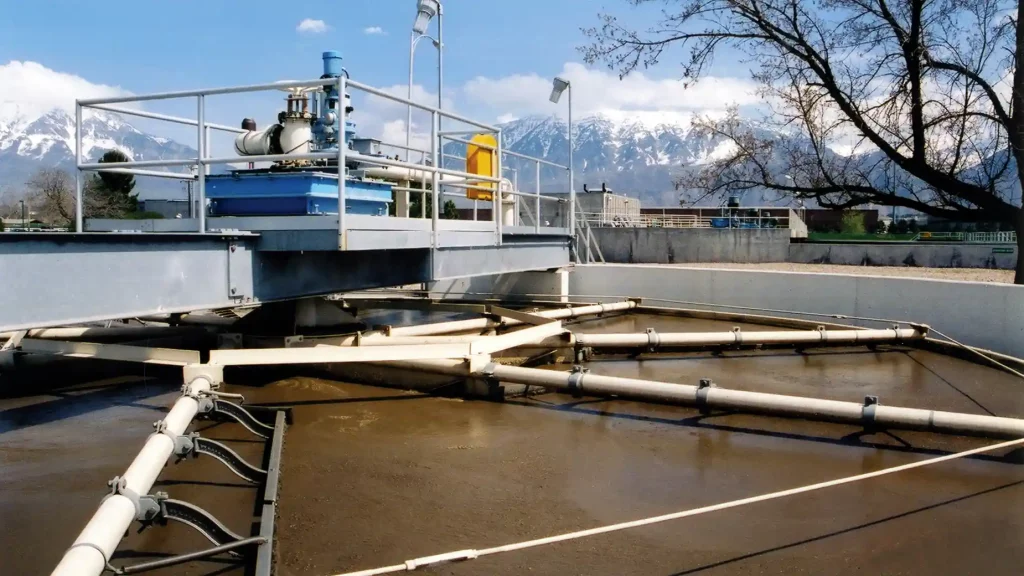
Flotation thickening is another method for the thickening of sludge. It involves the injection of tiny gas bubbles into the system to create artificial separation. The bubbles attach themselves to the solid particles, forming a gas-solid aggregate that is less dense than the surrounding liquid. This causes the aggregate to rise to the surface, where it can be skimmed off.
Dissolved air flotation (DAF) is a widely used method for thickening sludge. In this process, air is introduced into the wastewater through a rotating impeller or a porous material to create air bubbles.
The expected TS concentration of the sludge after thickening is 2 – 10%, depending on polymer use and type of pre-treatment.
Centrifugation
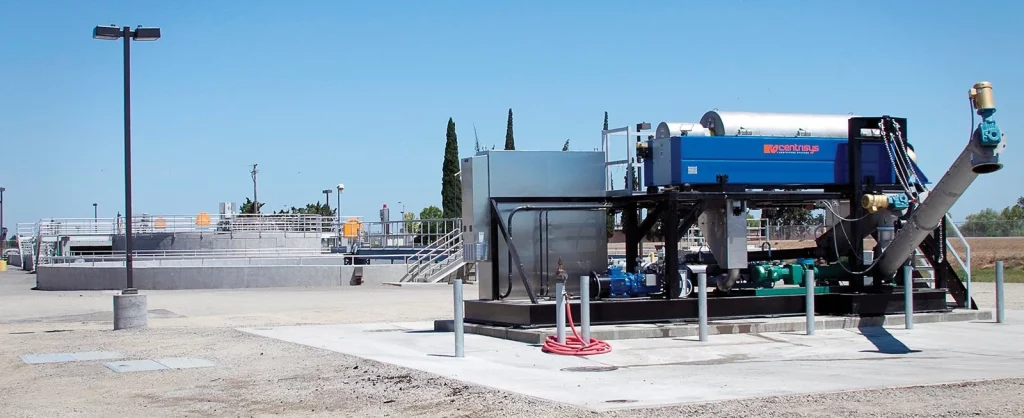
Sludge thickening can be achieved by utilising centrifugal forces. Centrifugation increases the centrifugal or artificial gravitational force, boosting the settling rate or velocity. The applied centrifugal force can be maintained by varying the rotation speed and the centrifugation chamber’s radius or diameter. However, the concentration of solids achieved by this process is relatively low. Therefore, chemical conditioning agents like polymers can increase the concentration of solids.
The expected TS concentration of the sludge after thickening is 16 – 35%, and polymer requirement can range from 5 – 40 g/kg of sludge depending on the type of pre-treatment and desired TS concentrations of the sludge.
Gravity Belt Thickening
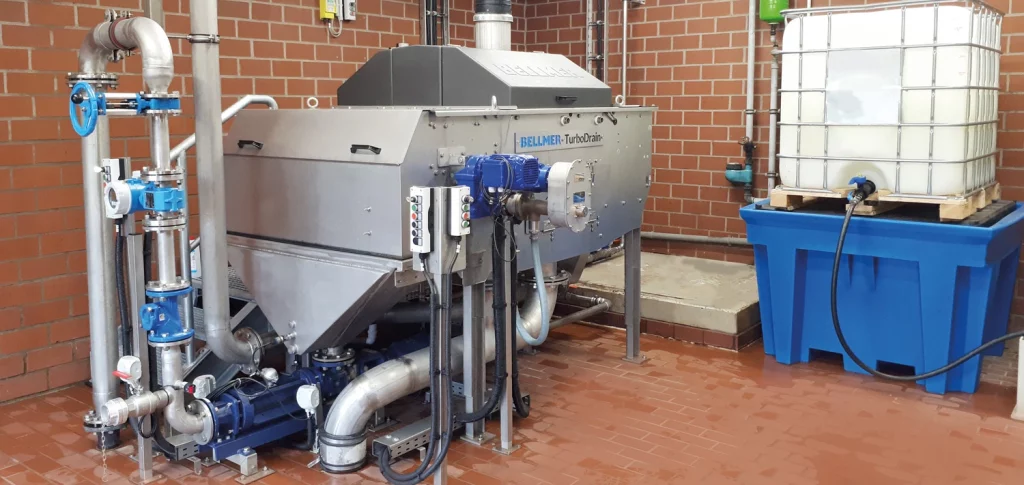
Gravity belt thickening separates solid and liquid sludge components through coagulation-flocculation while draining free water from the slurry using a moving fabric-mesh belt. The efficiency of this process is determined by sludge conditioning, which typically involves using a cationic polymer to neutralise the negative charge of the sludge solids. Compared to other mechanical sludge thickening procedures, gravity belt thickeners are known to be more cost-effective and energy-efficient.
The sludge is expected to have a concentration of 4 – 7% TS after thickening, and the required polymer amount can range from 1.5 – 6 g/kg of sludge.
Rotary Drum Thickening
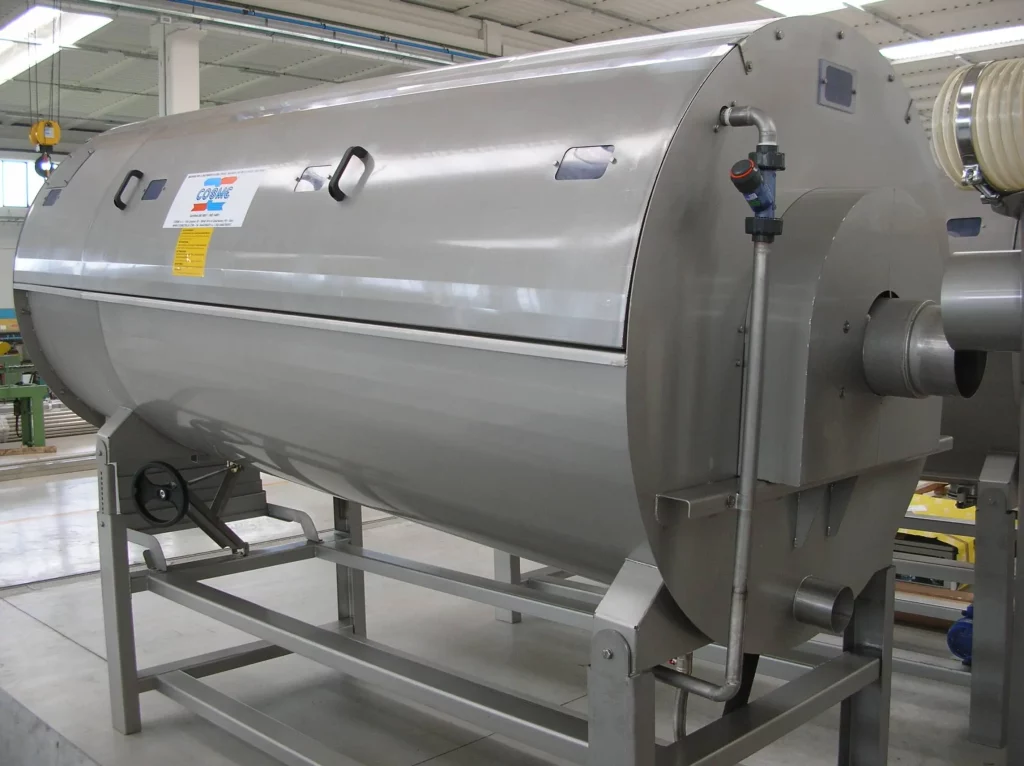
Rotary drum thickeners work by stirring solid sludge in a slowly rotating vessel with porous walls. This allows the free water or filtrate to drain out while the sludge is thickened via a rotating porous media. The porous wall can be made from polymers, steel, ceramics, or other materials. The cylindrical drum of a rotary drum rotates continuously while the sludge flows through it at a speed between 5 and 20 rpm. A spray system cleans the drum to prevent the pores from clogging.
The sludge is expected to have a concentration of 3 – 4% TS after rotary drum thickening. Polymer addition of 1 – 2.5 g/kg of sludge is necessary.
For further information, please click on the Materials tab at the top of the page.